HULK Metal is committed to mold making, forging blank forging, surface treatment, forging processing, quality inspection, etc. Every aspect of order production is 100% controlled. Zero defective forgings is our forging concept.

HULK Metal
Precision Hot Forging Service
-
Advantages
-
Capacities
-
Processes
-
Parts
-
Types
-
Factory
-
Introduction
-
Articles
-
Review
-
Top
START HOT FORGING SERVICES AT HULK METAL
We will continuously improve our hot forging service capabilities from the four aspects of hot forging factory, experience, quality and service, create first-class forging services for customers and improve customer satisfaction.
-
FACTORY:
HULK METAL has advanced hot forging facilities, strong machining capabilities, and staff with at least ten years of operating experience. We have produced and supplied customized forged parts for many fields. No matter what type of forging mold or parts you need, we All can be provided. If you have any need for customized forgings, please feel free to contact us for quotation.
-
Experience:
Our team is experienced and each member has undergone strict training. You can rest assured to place your order with us. HULK METAL can independently complete all processes from billet making - forging - heat treatment - machining - flaw detection - inspection. The manufacturing level Far ahead. If you are looking for an experienced hot forging shop, then contacting us is the right choice.
-
Quality:
HULK METAL has high-precision quality inspection and testing equipment, complete measurement methods, and unified inspection standards. At every stage of the order production process, we will conduct corresponding inspections to ensure the production of zero-defect forgings. Our commitment to quality assurance is that every product that leaves our facility meets or exceeds industry standards, giving our global customers peace of mind.
-
Services:
At HULK METAL, you can get top-notch services. We not only provide high-quality forgings and hot forging services, but also provide customers with accurate and easy-to-understand professional information. If you need custom forgings, trust us to provide exceptional service every forging, come experience our hot forging services today!
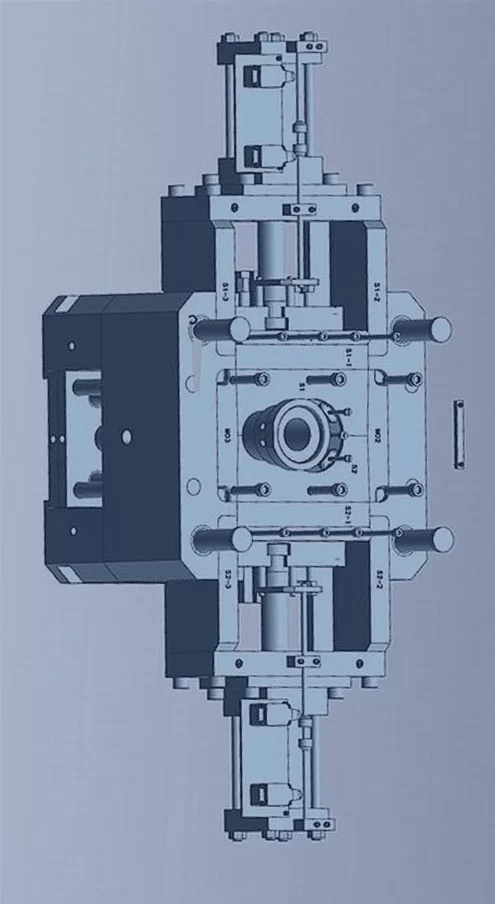
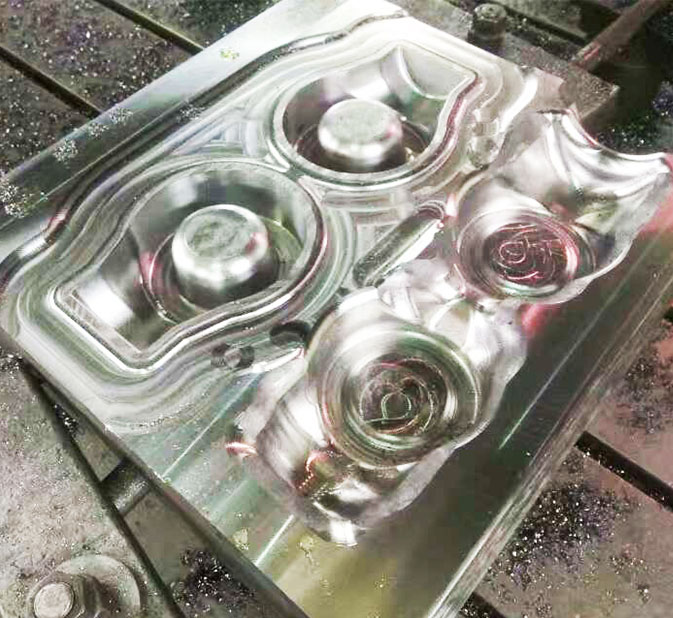
HOT FORGING SERVICES CAPACITIES
Here we will show you the relevant parameters of hot forging, including material, standards, tolerances, surface treatment and other essential key variables. This table is an important reference tool to ensure the accuracy, consistency and quality of forging operations. Please send your drawings and our technical team will conduct a comprehensive evaluation and provide you with a complete solution.
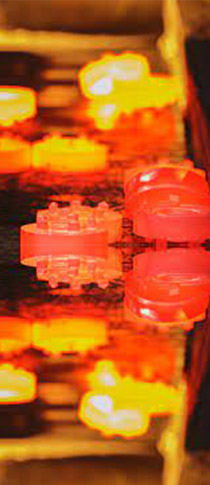
MANUFACTURING: | According To the Drawings and Samples |
SERVICE METHOD: | OEM |
MATERIALS:
| Carbon Steel, Alloy Steel, Cold and Hot Moulded Shell Steel, Stainless Steel, Heat-resistant Steel and Other High Alloy Steel Parts |
Product Size | Available As Customer's Drawing Required |
Color | Customer's Requirements |
Mould | Design and produce by ourself |
Standard | ISO, DB34/T 1240-2010 etc. |
Weight Range | 0.01-500KG |
Machining Precision | ±0.01mm |
Surface Treatment | Trimming, Deburring, Polishing, Shot Blasting, Sand Blasting, Tumbling, Powder Coating, Anodizing, Passivation, Chemical Coating, Painting, Electroplating, Electrophoresis and so on. |
Production Diagram | Drawings or Samples > Mold Fabrication > Mold Test > Qualified Sample > Mass Production Die Casting > Deburring > Drilling&Tapping > Polishing > CNC Machining > Surface Treatment > Printing Logo > Quality Inspection > Packing > Shipping. |
MOQ | 500KG / A Standard Tray |
HOW YOUR HOT FORGING PARTS PRODUCED
Here we will introduce you to the basic process flow of hot forging, including blanking, heating, deformation, cooling, inspection and other links. These links will give you a general understanding of hot forging. If you want to know more about hot forging services, you can contact us.
-
01
Customize Solutions
First, we will have professional engineers carefully analyze your drawings and provide professional quotations to ensure the accuracy and reliability of each project.
-
02
Mold Making
We offer a variety of custom molds to accommodate different batch sizes, materials and forging geometries. For small batch production, we choose molds with streamlined structures, which may have a shorter service life. For high-volume production, our molds feature a multi-step design that includes blank preparation, pre-forging and final forging stages to ensure extended mold life.
-
03
Forging Billet Blanking
Before heating and forging, we will determine the appropriate cutting method for the forging products based on the material's properties, size, and batch size, and cut the raw materials into reasonable sizes and lengths.
-
04
Heating
In order to increase the plasticity of the metal, reduce its resistance to deformation and facilitate the forging process while achieving optimal structural results, the metal must be preheated. Throughout the metal heating stage, as the temperature gradually increases, the metal material will undergo a series of transformations.
-
05
Hot Forging
After the metal blank is heated to a temperature higher than the recrystallization temperature of the material, the metal blank is plastically formed into the shape and size of the forging using a mold. Hot forging has always played an important role in shaping metal parts with precision, strength and efficiency.
-
06
Trimming
It is usually carried out at a temperature of not less than 800°C. Timely trimming after hot forging is completed can effectively reduce the risk of cracks at the shearing point and ensure the structural integrity and quality of the forged parts.
-
07
Finishing
In order to enhance the beauty of the workpiece by removing surface scale and burrs, a series of refining techniques are used. These methods may include grinding, sand blasting, shot blasting, pickling, etc. The most appropriate processing method will be flexibly selected based on factors such as the material composition and specific shape of the forging.
-
08
Heat Treatment
The most commonly used classification methods of heat treatment include normalizing, annealing, quenching, tempering and surface hardening. According to the production requirements of the drawing, we will choose the appropriate heat treatment method.
-
09
CNC Machining
The Engineering Committee bases on the specific materials, shapes, dimensions, surface requirements, and customary engineering techniques, such as turning, milling, tapping, drilling, etc.
-
010
Surface Treatment
We offer comprehensive surface treatment services to enhance product durability, corrosion resistance and aesthetics. Our expert team uses advanced technologies such as electroplating, spray painting, powder coating, shot blasting, etc. to meet different industry needs.
-
011
Quality Control
From the size, surface quality, and chemical composition testing of raw materials, to the testing of forging, cooling, and heat treatment during the production process, and finally to the size and shape of the finished product, and internal quality testing, we will conduct strict inspections on forgings at every step.
-
012
Warehousing
Our warehouse layout has been carefully designed to efficiently accommodate raw materials, semi-finished products, finished product processing, storage, combination packaging and delivery operations. It’s not only optimizes our workflow but also enhances our ability to provide additional value-added services to our clients, ultimately aiming to increase overall client satisfaction.
-
013
Packaging & Delivery
When it comes to packaging, we use industry-leading standards to protect our forged components during shipping. Each item is carefully packed and secured to prevent any damage on the way to your destination. Additionally, we work with reputable logistics providers, so whether you require local or international shipping, rest assured that your order will be handled with the utmost care.
-
014
After Service
For us, customer satisfaction goes beyond the point of purchase. Our dedicated after-sales service ensures seamless support for your forged products. Whether you need technical assistance, maintenance guidance or product replacement, our team of experts will meet your needs promptly and efficiently.
PARTS HULK METAL HOT FORGING FACTORY PRODUCED
The images provided in this article depict our products and are sourced from Internet platforms. It is important to emphasize that we adhere to strict confidentiality standards. Therefore, we will never disclose product images or specifications to any third party without the prior consent of our customers.
-
ACSR Cable Conductor Gripper
A Cable Conductor Gripper is an essential tool designed for use with steel wire, Aluminum Conductor Steel Reinforced (ACSR) wire, or insulated wire. This versatile product is engineered to meet a wide range of applications.
READ MORE
-
Wire Rope Gripper For Bare Aluminum
A Wire Rope Gripper is an essential mechanical component engineered to secure and stabilize steel or aluminum wire ropes, ensuring their safe and reliable use across various applications.
READ MORE
-
Wire Grips For Wire Rope
The wire grips for wire rope we produce are carefully crafted from high-strength alloy steel. Each wire grip undergoes a rigorous process during the manufacturing process, including hot forging, heat treatment, and precision machining.
READ MORE
-
Trailer Spare Parts
HULK Metal is committed to providing you with a variety of trailer spare parts to meet your diverse needs and application scenarios. Our extensive product line includes but is not limited to, hitches, brackets, wheels, braking systems, and connectors.
READ MORE
-
Shackle Hitch Receiver
HULK Metal's shackles are made of high-quality carbon steel, alloy steel, and stainless steel, with a safety factor of 4 to 6 times. A variety of specifications are available for you to choose from, and non-standard customization is supported.
READ MORE
-
Precast Concrete Accessories
Our lifting devices are carefully designed to solve situations where the load is too heavy to be lifted manually, or where the load needs to be lifted regularly and manual lifting would cause unnecessary stress to the operator.
READ MORE
More Results
METAL FORGING TYPES HULK METAL CAN SUPPLY
We use material classification as a means of simplifying the classification of hot forgings, ensuring our customers can easily find relevant information about metal forging materials. For further inquiries and to receive comprehensive solutions and pricing, we look forward to having you contact us.
Carbon Steel Hot Forging
Alloy Steel Hot Forging
Stainless Steel Hot Forging
-
Carbon Steel Hot Forging
Utilizing carbon steel as our primary raw material, we use a hot forging process to meet precise specifications in terms of dimensions, surface texture and performance attributes. Carbon steel is divided into low carbon steel, medium carbon steel and high carbon steel. For carbon structural steel, their forging temperatures will also be different. Our forging workers have more than ten years of operating experience and can accurately control the temperature during the forging process. We can provide you with competitive pricing, so please contact us as soon as possible.
-
Alloy Steel Hot Forging
We transform raw alloy steel into precision parts tailored to precise specifications of shape, size, surface finish and material properties. Once the alloy steel ingot is heated to optimal forging temperatures, our skilled craftsmen use a combination of hydraulic presses and hammering techniques to shape the metal with precision and finesse. This controlled deformation ensures our forged parts have the desired strength, elasticity and dimensional accuracy. Whether you require complex geometries, complex designs or high-strength components, our alloy steel hot forging process delivers unparalleled performance and reliability.
-
Stainless Steel Hot Forging
It is a process that transforms raw stainless steel into complex and durable parts through the application of heat and pressure. Stainless steel has the advantages of high strength, ductility, toughness, etc. Our technicians carefully control the temperature and pressure parameters to ensure the best forging conditions of stainless steel and improve its mechanical properties such as strength, toughness, and corrosion resistance. Partner with us for your stainless steel hot forging needs and experience the unparalleled quality and efficiency of our manufacturing process.
VIEW HULK METAL HOT FORGING FACTORY
We have advanced forging equipment, cutting-edge mold design and manufacturing capabilities, and professional quality control, which is why we are able to accurately and efficiently shape raw materials into complex and strong parts.If you need quality metal hot forging services, please feel free to contact us.
-
Equipment
We use high-capacity hydraulic forging presses that are able to exert tremendous force with unparalleled precision. An advanced induction heating system complements our hydraulic presses and is carefully calibrated to provide even heating of a variety of materials.
-
Production Team
Operators have extensive knowledge and experience in hot forging technology, materials and machine operations.
-
QC Center
Our QC center has impact testing machines, salt spray testers, hardness tester, flaw detector to issue material and product testing reports according to your requirements.
HOT FORGING SERVICES INTRODUCTION
Here we will introduce to you what hot forging is, what are the advantages and disadvantages of hot forging, and through the following explanation, you will have a basic understanding of metal hot forging services.
-
Hot Forging Services Means
Hot forging is a manufacturing process that involves shaping a metal while heating it to a high temperature, usually above its recrystallization point. According to the forging temperature, it can be divided into hot forging, cold forging and warm forging. This classification scheme emphasizes forging above the recrystallization temperature (hot forging), below the recrystallization temperature (warm forging), and at room temperature or without heating (cold forging). HULK METAL specializes in hot forging, by heating metal to a malleable state and using molds and presses to precisely shape it, ensuring the consistency and accuracy of each product.
-
Advantages and Disadvantages of Hot Forging
Advantages:
1. Increased material strength. 2. Allow strict tolerances. 3. Higher productivity. 4. Improved grain structure and enhanced mechanical properties.
Disadvantages:
1. The complexity of parts is limited. 2. The mold is easy to wear and needs to be repaired later.
HULK Metal also manufactures standardized products such as handrails and guardrails systems, concrete precast accessories, glass clamps, and aluminum-plastic panels.
ARTICLE OF HOT FORGING
We have curated a selection of informative articles on the complex process of hot forging, covering a range of topics including raw materials, forging methods, complex processes, and a detailed exploration of their respective advantages and disadvantages. We invite you to delve deeper into the world of forging, gain a deeper understanding of its many dimensions, and become familiar with our comprehensive service package. To further explore forging technology and find out more about the range of services we offer, please contact us.
-
July 01, 2024
Difference between hot forging and cold forging
READ MORE
-
June 27, 2024
What are the advantages and disadvantages of the hot forging process?
READ MORE
-
January 18, 2024
Forging: What Is It? What Are The Different Types of Hot Forging?
READ MORE
-
July 03, 2024
What are the processes of hot forging?
READ MORE